13 Mar Primii cinci ucigași ai productivității din industria PCB
Câteva soluții
Calea către maximizarea productivității fabricii constă într-o abordare de sus în jos care abordează punctele operaționale detaliate din secțiunile anterioare. Trebuie făcuți pași în următoarele domenii: Pregătirea datelor Simularea procesului de fabricație Pregătirea procesului de fabricație Sisteme de execuție a producției Sunt necesare soluții tehnice pentru toate aceste provocări. Și, în mod crucial, trebuie să existe sisteme de raportare pentru ingineri, operatorii de linie și managerii de producție, care identifică acțiunile specifice care trebuie întreprinse pentru a îmbunătăți performanța. Mai mult, informațiile trebuie să fie suficient de oportune pentru a permite îmbunătățiri înainte ca oportunitatea să fie pierdută și să apară noi probleme în altă parte. Pregătirea datelor Atenția acordată pregătirii datelor atât pentru introducerea modelului componentelor, cât și pentru introducerea datelor de proiectare este un prim pas obligatoriu: Modelarea componentelor – Producătorii trebuie să pună în aplicare modelarea fizică precisă a tuturor pieselor pe care intenționează să le folosească pe linie, inclusiv contactele pin pentru lipire. îmbinări, integrate cu datele CAD. Aceasta ar trebui să cuprindă: Modelarea consecventă, neutră în bibliotecă CAD, a pieselor pentru a permite DFM standardizat și funcții de pregătire a procesului în aval. Compensarea componentelor, rotațiile și declarațiile de polaritate normalizate la un standard. Industria electronică la nivel mondial are vânzări de 750 de miliarde de dolari, dintre care două treimi sunt reprezentate de ansamblul PCB. Producția de PCB este caracterizată printr-un impuls obsesiv pentru creșterea productivității în contextul a trei factori semnificativi din industrie: Cicluri de viață mai scurte ale produselor – Se exercită presiune pentru a dezvolta produse mai bune și a le aduce pe piață înainte ca concurența să o facă, la costuri mai mici, în timp ce se dezvoltă simultan produs de generația următoare. Cu doar cinci ani în urmă, ciclurile de viață ale produselor erau măsurate în ani; acum sunt măsurate în luni, punând presiune pe designeri și producători pentru a accelera procesul de trecere de la stadiul de prototip la fabricarea în volum mare. Mai multă complexitate – Producătorii produc modele mai complexe, cu densitate mai mare, cu miniaturizare sporită și plăci mai sofisticate. O listă de materiale (BOM) tipică pentru un ansamblu PCB poate avea acum mii de piese în total, formate din sute de elemente rând unice. Articolele „cumpărate” – condensatoare, rezistențe, diode și așa mai departe – vor avea fiecare una sau mai multe „piese alternative” pentru a permite costul minim al BOM și disponibilitatea maximă a pieselor. Listele de materiale mai complexe (BOM) pun un prim rang pe o calitate sporită a componentelor și o mai bună trasabilitate. Externalizarea crește rapid – Ciclurile de viață mai scurte ale produselor și complexitatea crescută i-au forțat pe OEM să adopte externalizarea, acum segmentul cu cea mai rapidă creștere din industria PCB. Companiile Electronics Manufacturing Service (EMS) reprezentau 21% din piață în 2004, dar cota lor va ajunge la aproximativ 30% până în 2008. În acea perioadă, piața va crește cu doar 16%. Furnizorii de EMS oferă prețuri mai mici, viteză accelerată de lansare pe piață și performanțe mai bune de onorare a comenzilor, deoarece valorifică puterea de cumpărare agregată masivă derivată din deservirea a sute de clienți diferiți și prin consolidarea activelor lor de producție și gestionarea acestora pentru a atinge costul unitar minim. Furnizorii de EMS se concentrează pe competența lor de bază de producție și achiziție de componente; OEM-urile sunt libere să se concentreze pe proiectarea și comercializarea de produse noi. Aceste tendințe din industrie sunt bine înțelese și au contribuit la transformarea ansamblului PCB într-una dintre cele mai competitive industrii din lume. Având presiunea de a reduce costurile, îmbunătățind simultan randamentele și viteza de intrare pe piață, se caută acele modificări ale operațiunilor din fabrică care pot îmbunătăți competitivitatea. De obicei, 60-70% din capitalul investit de active fixe în operațiunile de asamblare PCB este blocat în mașinile din liniile de asamblare. Asamblarea SMT necesită o mare intensitate de capital, de exemplu, cu linii unice care costă mai mult de 1 milion USD și prețul este în creștere. Managerii de fabrici de producție apăsați greu se întreabă cum se pot asigura că capitalul lor investit oferă productivitate și competitivitate maxime. Răspunsul se află nu numai la nivelul mașinilor individuale, ci și la nivelul întregii linii sau al fabricii. Asamblatorii PCB folosesc multe măsurători ale performanței de fabricație, de la specificul produsului secundar al timpului ciclului, rata de bataie a liniei și randamentul la prima trecere, până la repere de nivel superior, cum ar fi „costul de conversie a BOM” și rentabilitatea capitalului angajat. Indiferent de indicatori cheie de performanță (KPI) utilizați, scopul este de a genera producția maximă de produse de calitate acceptabilă din liniile de asamblare, materialele, instalațiile și resursele umane disponibile disponibile.
- Părți haos
- Configurare ineficientă a liniei
- Rate de bătaie mai lente decât optime
- Performanță scăzută a mașinii de vârf
- Combinația PCB/proces este sub-optimă
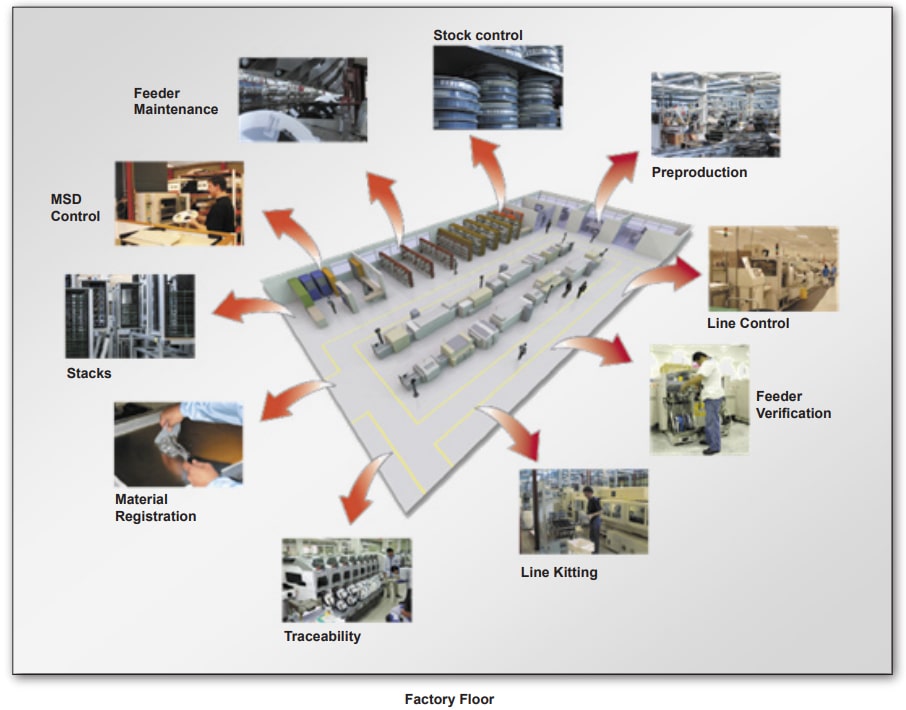
- Haosul pieselor Prima problemă care afectează productivitatea este că materialele nu sunt la locul potrivit la momentul potrivit, gata de utilizare pe liniile de asamblare. Mulți cred că este suficient să aveți o acoperire completă în ERP sau în sistemul de control al stocurilor principale a tuturor BOM-urilor care urmează să fie asamblate. Dar factorul critic este de a avea cantitățile corecte de piese și materiale disponibile și instalate pe mașini la momentul exact când este necesar. Verificarea disponibilității în masă a numerelor de piese ale componentelor nu previne eșecul fabricării din cauza indisponibilității pieselor la nivelul fabricii, deoarece:
i. Piese deja angajate în alte configurații – Componentele pentru asamblarea pe PCB-uri sunt de obicei manipulate în vrac – fie în bobine care conțin mii de piese, fie în stive de tăvi care dețin sute. Dacă aceleași piese sunt necesare simultan pentru două comenzi de producție, nicio linie nu poate fi configurată corect. Înmulțirea impactului acestei probleme pe sutele de role de componente sau tăvi prezente pe o podea tipică a unei fabrici de PCB, mărește riscul de a nu putea livra cantitățile potrivite de piese la linii pentru fiecare comandă de producție, în ciuda faptului că, în total , cantitățile totale de piese necesare pentru comenzile de producție se potrivesc cu cantitățile totale de piese din sistemul de control al stocului principal.
ii. Piesele disponibile nu pot fi găsite – Adesea, în fabricile mari, sistemele ERP nu urmăresc materialele foarte precis odată ce sunt eliberate la nivelul producției. Datele cheie – referitoare la linia căreia sunt alocate piesele, dacă configurațiile pentru care sunt angajati sunt încă în producție și cantitatea exactă de piese care au fost legate în acele setări – lipsesc frecvent. Deși datele disponibile arată că piesele sunt disponibile pentru a începe producția, acestea nu pot fi localizate frecvent. Întârzierile inutile apar la începutul unei rulări de producție, în timp ce „expeditorii” caută frenetic materialul lipsă. În egală măsură, și din cauza aceleiași lipse de vizibilitate a piesei unde se află, adesea piesele pot fi livrate inutil către o linie, pentru a sprijini configurarea, atunci când de fapt o aprovizionare suficientă din acele piese este deja încărcată pe linie, rămase de la un comanda anterioară de producție. Aceste inexactități de urmărire duc la creșteri inutile ale costului inventarului din fabrică. din cauza greșelii sau defecțiunii duzei înainte de plasare. În general, acest lucru îi obligă pe producătorii de PCB-uri să supraestimeze
III. Piese în carantină – Un alt factor care afectează disponibilitatea pieselor la mașina de preluare și plasare este sensibilitatea unor categorii de componente la expunerea la condițiile atmosferice normale de pe podeaua fabricii. Uneori componentele sunt afectate de umiditatea atmosferică după despachetarea din recipiente sigilate și, după doar câteva ore, acestea trebuie coapte în cuptor pentru a elimina umezeala din corpurile componente. Discontinuitățile cauzate de ciclurile de coacere în cuptor înseamnă că anumite piese trec prin cicluri de a fi „disponibile” și „indisponibile” pentru asamblare, deși sunt „în stoc” tot timpul.
iv. Control inexact al stocurilor – Disponibilitatea stocului de piese deținută în sistemul ERP este adesea inexactă ca urmare a risipei neînregistrate. Atunci când componentele sunt returnate la depozit după utilizare la etajul fabricii, adunarea unei imagini precise a câte piese rămân pe bobină este problematică. Ar trebui managerii de producție să ia pur și simplu cantitatea inițială și să deducă numărul de plasamente definite în lista de materiale? Probabil că nu, deoarece ignoră piesele pierdute de nivelul stocului mașinii, ceea ce duce la epuizări neașteptate de stoc la nivelul fabricii în comenzile de producție ulterioare. Opririle de producție costisitoare (și neplanificate) ca acestea creează nevoia de a curăța materialele din linii pentru comenzile ulterioare și achiziționarea urgentă de piese pentru a corecta lipsurile. Controlul inexact al stocurilor forțează, de asemenea, practica consumatoare de timp și costisitoare a auditurilor de inventar la nivel de amplasament, atunci când producția este, în esență, suspendată în timp ce înregistrările din sistemul ERP sunt sincronizate manual cu realitatea etajului de producție.
v. nivelurile stocurilor, ducând la epuizări neașteptate de stoc la nivelul fabricii în comenzile de producție ulterioare. Opririle de producție costisitoare (și neplanificate) ca acestea creează nevoia de a curăța materialele din linii pentru comenzile ulterioare și achiziționarea urgentă de piese pentru a corecta lipsurile. Controlul inexact al stocurilor forțează, de asemenea, practica consumatoare de timp și costisitoare a auditurilor de inventar la nivel de amplasament, atunci când producția este, în esență, suspendată în timp ce înregistrările din sistemul ERP sunt sincronizate manual cu realitatea etajului de producție.
- Configurare ineficientă a liniei O linie de asamblare SMT eficientă depinde de capacitatea de a coordona sute de variabile de configurare simultan. Dacă orice aspect al configurației liniei este incorect, rezultatul este o calitate slabă. Există mai multe motive comune pentru configurarea și depanarea liniei lente:
i. Instrucțiunile de configurare nu se potrivesc cu programele mașinii – În multe cazuri, datele de inginerie care sosesc pe linii provin din fluxuri de date multiple, deconectate. Lista de echipamente pentru fiecare mașină este condusă de la BOM în sistemul ERP, dar nu ia în considerare deciziile de împărțire și echilibrare a BOM luate de programatorii mașinii. Sistemele CAM utilizate pentru generarea programelor de mașină funcționează adesea dintr-o bază de date diferită de sistemul CAM utilizat pentru a genera dispozitivul de călătorie de etaj din fabrică. Și sistemele CAM utilizate pentru programarea mașinilor AOI sunt diferite de sistemele utilizate pentru programarea mașinilor de pick and place. Fragmentarea fluxurilor de date poate fi extinsă; fiecare punct de deconectare dintre bazele de date de inginerie oferă o altă oportunitate de a genera date sau instrucțiuni nesincronizate pentru diferite părți ale liniilor de asamblare. Toate erorile de configurare trebuie fie eliminate la sursă, prin proiectare, fie descoperite la prima etapă și eliminate prin editarea instrucțiunilor de configurare în timp ce linia este în jos și neproductivă.
ii. Datele pieselor de pe mașini lipsesc sau sunt incorecte – Fiecare mașină SMT pick and place, mașină AOI și tester în circuit are nevoie de o bibliotecă de date pentru a descrie caracteristicile cheie ale fiecărei componente care urmează să fie asamblate, inspectate sau testate. Doar atunci când biblioteca de componente a mașinii este plină cu date care descriu componentele pentru comanda de producție, mașina își poate face treaba. Fiecare piesă nouă încărcată în fabrică înseamnă că datele din bibliotecă pentru acea parte trebuie introduse în mașini și verificate. Odată create, datele trebuie, de asemenea, să fie gestionate corespunzător, deoarece orice modificări care sunt făcute pot duce la timpi inutil de nefuncționare dacă nu sunt efectuate de un operator calificat. Fără o soluție controlată și centralizată pentru a gestiona datele componentelor la nivel de mașină, datele trebuie introduse cu minuțiozitate în mai multe mașini, cauzând timpi inutil de nefuncționare și un risc ridicat de consecvență a datelor între mai multe mașini.
iii. Configurarea offline completă nu este realizată – Mulți producători nu sunt capabili să încarce componente offline și să configureze verificarea. Acest lucru forțează demontarea și configurarea liniei să fie întreprinse înainte ca producția să poată începe, ceea ce duce la timpi de nefuncționare risipitoare. Fără îndoială, costul total al inventarului alimentatorului poate fi minimizat prin efectuarea configurației on-line, dar se plătește un preț mare în ceea ce privește pierderea producției de linie și utilizarea mașinii.
iv. Configurarea este incorectă la prima etapă – Dacă configurarea generală a liniei nu este verificată în paralel cu verificarea inventarului de la început, erorile trebuie detectate în momentul producerii primei. Acesta este cel mai costisitor mod de a găsi și elimina o eroare de configurare, deoarece timpul scurs între crearea erorii și detectare este maximizat. Înmulțiți oportunitățile de eroare/detectare/remediere în funcție de numărul de alimentatoare, mașini, programe, iar oportunitatea de a escalada timpul de depanare a configurației devine clară, în comparație cu verificarea fiecărui aspect al configurației pe măsură ce este efectuată. Odată ce prima etapă este finalizată și linia este în plină producție, este de asemenea esențial ca erorile să fie evitate atunci când piese noi sunt montate pe o mașină pentru a reumple un alimentator epuizat. În cel mai rău caz, piesele plasate incorect vor fi detectate după asamblarea lotului complet, în etapa de inspecție sau de testare. Astfel de reparații au costuri maxime și impact asupra productivității generale a instalației.
v. Eșecul de a exploata configurațiile existente ale mașinii – Cea mai bună modalitate de a minimiza timpul de nefuncționare a configurației este de a elimina necesitatea de a demonta liniile și de a le configura din nou între comenzile de producție. Datorită complexității gestionării varietății uriașe de componente, alimentatoare, poziții de alimentare, cantități de componente și factorii care afectează o configurație optimizată pentru un timp minim de ciclu, majoritatea producătorilor scot toate alimentatoarele și componentele din liniile dintre comenzile de producție. Acest lucru menține controlul, dar reduce dramatic productivitatea. Analizând în avans comenzile de producție și identificând grupuri de produse care pot împărtăși aceeași configurație (sau majoritatea configurației) pe o linie de asamblare, fără a sacrifica rata de bataie într-un grad inacceptabil, pot fi realizate economii masive în timpul de nefuncționare. Folosirea tehnicilor de grupare a produselor oferă îmbunătățiri semnificative ale productivității în operațiunile de mix mare/volum mic spre mediu, unde schimbările sunt unul dintre cei mai importanți factori care contribuie la oprirea liniei.
văzut. Eșecul anticipării cerințelor de reaprovizionare a pieselor – În medii de producție cu volum mare și amestec redus, lipsă de avans pentru o abordare precisă bazată pe simulare pentru programarea liniei în ansamblu. ii. Programarea mașinii nu se bazează pe simularea cinematică completă – Dacă simularea la nivel de linie și programarea (echilibrarea) sunt separate de programarea mașinii, va exista conflict între cele două; echilibrarea depinde de informații precise despre timpii de ciclu individuali, iar programarea mașinii poate genera un timp de ciclu al mașinii diferit de cel asumat de funcția de echilibrare a liniei. Cheia este simularea foarte precisă a configurației fiecărei mașini (alimentatoare, duze, ...) și a cinematicii mișcării acesteia. Fără acuratețe în simularea timpului de ciclu al mașinii, nu numai că performanța individuală a mașinii va avea de suferit, dar și linia generală nu va fi echilibrată pentru o producție generală optimă. vizibilitatea necesității de a reumple piese de pe linie este cea mai importantă cauză a timpului de nefuncționare. Cel mai rău caz apare atunci când toate componentele dintr-un alimentator sunt epuizate, dar este o surpriză pentru operatorul de linie (care trebuie să supravegheze sute de alimentatoare simultan). Acest lucru forțează linia în jos în timp ce alimentatorul este scos, o nouă bobină este încărcată (presupunând că este la îndemână) și alimentatorul este reîncărcat pe mașină.
- Rate de bataie mai lente decât optime Odată ce liniile au fost configurate, producția se instalează în ritmul repetabil, cu PCB-uri asamblate care ies de pe linie la o frecvență fixă determinată de echilibrul liniei, capacitățile mașinii și nivelul de optimizare încorporat în produs. programele specifice ale mașinii în sine. În acest moment, productivitatea este afectată într-un mod costisitor, dar invizibil, dacă liniile nu sunt programate să ruleze la rata maximă posibilă. Acest lucru se poate întâmpla din mai multe motive: i. Simularea, împărțirea/echilibrarea BOM și programarea mașinii nu sunt efectuate la nivel de linie completă – Mașinile individuale pot fi programate la un nivel optim, dar dacă nu se adoptă o abordare completă a sarcinii de programare, pe baza unei simulări cinematice complete. dintre toate mașinile care alcătuiesc linia, performanța generală are de suferit, cauzată în primul rând de dezechilibrele din volumul de lucru al mașinilor. Durata ciclului, sau rata de bătăi, a liniei este determinată de cea mai lentă mașină din linie, subliniind necesitatea unei abordări precise bazate pe simulare pentru programarea liniei ca întreg.
ii. Programarea mașinii nu se bazează pe simularea cinematică completă – Dacă simularea la nivel de linie și programarea (echilibrarea) sunt separate de programarea mașinii, va exista conflict între cele două; echilibrarea depinde de informații precise despre timpii de ciclu individuali, iar programarea mașinii poate genera un timp de ciclu al mașinii diferit de cel asumat de funcția de echilibrare a liniei. Cheia este simularea foarte precisă a configurației fiecărei mașini (alimentatoare, duze, ...) și a cinematicii mișcării acesteia. Fără acuratețe în simularea timpului de ciclu al mașinii, nu numai că performanța individuală a mașinii va avea de suferit, dar și linia generală nu va fi echilibrată pentru o producție generală optimă.
iii. Datele pieselor la nivel de mașină nu sunt programate pentru o performanță optimă de manipulare – Datele pieselor utilizate de fiecare mașină definesc modul de manipulare a componentelor: cu ce viteză, cu ce duză, cât de lungă ar trebui să fie diferiții timpi de stație, ce compensații ar trebui să se aplice. punctul de preluare și așa mai departe. Completarea primului lucru este suficientă pentru a verifica dacă produsul este asamblat corect, dar acest lucru nu expune niciun efect al vitezei reduse de asamblare din cauza instrucțiunilor de manipulare suboptimale încorporate în biblioteca de date de piese a mașinii. Un operator va alege uneori să reducă viteza de plasare a unei componente pentru a asigura asamblarea, mascând adesea problemele de întreținere care ar trebui abordate, reducând în același timp productivitatea generală a liniei. Ca și în cazul optimizării programelor mașinii în sine, fără acces la date detaliate de performanță este practic imposibil pentru oameni să identifice aceste efecte; iar fără detectare nu pot fi corectate.
- Performanță scăzută a mașinii de vârf Cu investiții în linii de milioane de dolari, este clar că mașinile trebuie menținute pentru a funcționa la productivitate maximă pentru timpul maxim. Cu toate acestea, există multe aspecte ale stării mașinii care au un efect insidios asupra scăderii performanței generale.
- Presiunea de vid a duzei – Dacă aceasta este în afara specificațiilor, face ca componentele să fie scăpate în tranzit între punctul de preluare și poziția lor pe PCB.
- Comutarea vidului duzei lipicioase – Dacă comutatorul vacuumului este lipicios, duce la salturi ale duzei. Pentru a alege fără eroare componentele din alimentator necesită o comutare pozitivă și rapidă a alimentării cu vid la duze. Același lucru este valabil și pentru plasare; comutarea lentă sau imprecisă a vidului determină preluarea sau plasarea imprecisă.
- Hrănitori uzați – Acest lucru duce la rate ridicate de pierderi de ridicare. Alimentatoarele de componente sunt dispozitive mecanice de indexare care se uzează în timp. Pe măsură ce mecanismul se uzează în timpul utilizării normale, acuratețea prezentării componentei pentru preluare scade, ceea ce duce la eșecul de a ridica corect, ceea ce irosește componentele și timpul ciclului. iv. Instrucțiuni de întreținere slabe – liniile SMT plasează componentele la viteze de zeci sau sute de mii de piese pe oră. Această viteză a mașinii fulgerului face dificilă observarea performanței în scădere. Alegerile greșite apar prea repede pentru a fi văzute, dar o întârziere de câteva milisecunde a unei funcții care se repetă duce la o performanță detonată. Fără o notificare precisă și în timp util a locului în care se află scăderile de performanță, operatorii de linie și personalul de întreținere au șanse mici de a lua măsurile potrivite pentru a crește performanța.
- Instrucțiuni de întreținere slabe – liniile SMT plasează componentele la viteze de zeci sau sute de mii de piese pe oră. Această viteză a mașinii fulgerului face dificilă observarea performanței în scădere. Alegerile greșite apar prea repede pentru a fi văzute, dar o întârziere de câteva milisecunde a unei funcții care se repetă duce la o performanță detonată. Fără o notificare precisă și în timp util a locului în care se află scăderile de performanță, operatorii de linie și personalul de întreținere au șanse mici de a lua măsurile potrivite pentru a crește performanța.
- viteza mașinii fulgerului face dificilă observarea performanței în scădere. Alegerile greșite apar prea repede pentru a fi văzute, dar o întârziere de câteva milisecunde a unei funcții care se repetă duce la o performanță detonată. Fără o notificare precisă și în timp util a locului în care se află scăderile de performanță, operatorii de linie și personalul de întreținere au șanse mici de a lua măsurile potrivite pentru a crește performanța.
- Combinația PCB/proces este suboptimă. PCB-urile pot fi proiectate pentru a fi prietenoase cu procesul de asamblare sau ostile procesului. Cele mai multe PCB-uri pot fi asamblate în cele din urmă, dar costurile mai mari decât cele necesare din cauza designului suboptim, nivelurile de reluare și eficiența liniei variază ca urmare a caracteristicilor de proiectare, cum ar fi:
i. PCB-ul nu este prietenos cu mașinile sau liniile – Elementele de referință sunt ascunse, componentele intră în conflict cu transportoarele, designul panoului de asamblare nu este prietenos cu optimizarea. Constrângerile de proiectare, cum ar fi distribuția componentelor pe placă sau varietatea BOM, sunt de așa natură încât un tip de mașină nu poate atinge un cost de plasare scăzut și acest lucru nu devine vizibil până când produsul rulează pe linie.
ii. Designul șablonului de lipit duce la îmbinări de lipire suboptime - Acest lucru are ca rezultat o reluare ridicată. Obiectivul principal al asamblarii este de a crea îmbinări de lipire fiabile. În afară de un control bun asupra procesului de lipire, combinația dintre știftul componentei, modelul tampon și deschiderea șablonului de lipit trebuie optimizată pentru a oferi procesului cea mai bună șansă de a realiza îmbinări care se încadrează în toleranțe acceptabile (măsurate de obicei în zeci de îmbinări slabe, pe milion fabricat).
iii. Dispunerea PCB-urilor încurajează arcul și răsucirea – Panourile PCB-urilor încărcate pe linie pentru asamblare ar trebui să fie perfect plane, astfel încât să se evite „închiderea” transportorului și erorile de procesare în mașini. Prin proiectarea PCB-ului cu o distribuție uniformă a cuprului în toate axele, tendința PCB-ului de a se înclina și de a se răsuci în timpul procesării va fi minimizată.
iv. Modelele de plăcuțe/șină încurajează tombstoneing în timpul refluxului – Cu tendința către componentele de cip pasive mai mici, cum ar fi pachetele 0201, care sunt acum gestionate în volum, designul modelelor de plăcuțe și șenile pentru a permite efecte egale de absorbție a căldurii pe fiecare parte a componentei este de importanţă crescândă. Pe măsură ce componentele devin mai ușoare, efectul efectelor tensiunii superficiale în timpul refluxului devine mai important; dacă o parte se revarsă înaintea celeilalte, tensiunea superficială poate provoca ridicarea părții uscate a articulației, provocând efectul de „piatră funerară”.
Câteva soluții
Calea către maximizarea productivității fabricii constă într-o abordare de sus în jos care abordează punctele operaționale detaliate din secțiunile anterioare. Trebuie făcuți pași în următoarele domenii: Pregătirea datelor Simularea procesului de fabricație Pregătirea procesului de fabricație Sisteme de execuție a producției Sunt necesare soluții tehnice pentru toate aceste provocări. Și, în mod crucial, trebuie să existe sisteme de raportare pentru ingineri, operatorii de linie și managerii de producție, care identifică acțiunile specifice care trebuie întreprinse pentru a îmbunătăți performanța. Mai mult, informațiile trebuie să fie suficient de oportune pentru a permite îmbunătățiri înainte ca oportunitatea să fie pierdută și să apară noi probleme în altă parte. Pregătirea datelor Atenția acordată pregătirii datelor atât pentru introducerea modelului componentelor, cât și pentru introducerea datelor de proiectare este un prim pas obligatoriu: Modelarea componentelor – Producătorii trebuie să pună în aplicare modelarea fizică precisă a tuturor pieselor pe care intenționează să le folosească pe linie, inclusiv contactele pin pentru lipire. îmbinări, integrate cu datele CAD. Aceasta ar trebui să cuprindă: Modelarea consecventă, neutră în bibliotecă CAD, a pieselor pentru a permite DFM standardizat și funcții de pregătire a procesului în aval. Decalajele componentelor, rotațiile și declarațiile de polaritate normalizate la un standard.
Fara comentarii